7 essential features for your stock control solution
“A place for everything and everything in its place.”
This saying is at the heart of what stock control solutions should achieve, ensuring that the stock an organisation carries is always there when it is required.
But, for companies carrying a significant amount of inventory, across multiple sites, with levels changing day after day, stock control systems have to deliver so much more than the bare essentials.
With this in mind, we’ve collected what we consider to be 7 critical components you should look for in a stock control solution, to maximise the efficiency and effectiveness of how you manage inventory.
What is a stock control system?
At its core, a stock control system allows you to track products and equipment throughout your company’s supply chain. Through this, you should be able to map the entire journey of a product, from the moment an order is placed to when it leaves your stock for good.
However, the very best stock control solutions can offer so much more than this, as we’ll illustrate further in the article. We are constantly refining our own solution to give customers not only complete oversight of their stock levels, but can generate data to help them plan and project for the future.
Why is a stock control solution so important?
Imagine a vital piece of equipment in your building, perhaps a generator or server, suddenly fails. Without a replacement in stock, or the right parts to support the repair of this equipment, you will be left waiting for these to arrive.
This downtime could compromise how efficiently your team can work, causing costs to creep up while you can’t function as you normally would. This is a worst-case scenario, but it is a very real possibility for companies that don’t have a handle on their inventory at any given point in time.
Which makes it worrying that, as of 2017, only 18% of SMBs employed a form of this software.
Plus for industries such as retail, the warehouse is the backbone of their organisations. When 70% of online shoppers will typically look elsewhere for an item rather than wait for it to return to stock at the original destination, it is critical they have total oversight of their inventory levels to make sure they don’t miss out on potential business.
Because of how critical these systems are for organisations worldwide, below we have identified 7 essential functions that your stock control solution should incorporate to bring the biggest benefits to your business.
1. End-to-end, real-time inventory monitoring
The primary objective of any stock control solution is to give you complete insight into all goods and items you have in stock at any moment in time. Not last week. Not even yesterday. Right this second.
A Cloud-based, real-time solution is vital because whenever changes are made, you need to know. As noted earlier, if an emergency situation demands an asset or component that is no longer in your possession, the wait for a replacement can be painful for productivity and your budget.
Whether stock has been ordered and acquired by your customers, or utilised by your FM team for work across your site, this needs to be tracked and noted immediately, so that purchase orders can be sent out to restock these.
In addition, an effective stock control system should allow you to establish your own parameters for when a category of items needs to be replenished. Once it dips below a certain level, a notification can then be delivered to those responsible for arranging reorders, or better yet, a purchase order can be automatically sent out by your system, freeing more burden from your team.
Why you need this: To ensure your stock is always at appropriate levels, allowing your team and facilities to operate at optimal efficiency.
2. Instant tagging and barcode scanning
In order to enhance your ability to keep tabs on what assets are in stock at any given time, a stock control solution should allow you to tag every individual item, and log it within the system. This allows you to identify when a product arrives, throughout its time in storage, and when it is either delivered to a customer or taken by someone on your team.
By tagging assets, and using these tags to group these together into fitting categories, it makes it far faster for your team to perform accurate stock takes and valuations.
This can be improved further by incorporating a barcode scanner. Using a mobile device, someone can scan the barcode of any asset and be presented with all its essential details and history. Through this, you can determine how long an asset has been in storage, and whether it requires replacing due to this.
Furthermore, effective tagging will also give your team a clear sense of what items need to be replenished most often, and which are barely (if ever) taken, which could then guide your approach to restocking these for the most cost-effective outcome.
Why you need this: To reduce asset downtime and build a complete understanding of the assets you have in stock at any given time.
3. A single, easy-to-use interface
A stock control solution is only as useful as your team’s ability to use it. Therefore, ensuring your solution is straightforward for your employees is crucial to reaping the full benefits of this technology, and guaranteeing it will be used consistently.
You shouldn’t need to give your team weeks upon weeks of training and hand them a bulky, incomprehensible manual to use the system day-to-day. Instead, its various functions and features should be simple to pick up, and the data it delivers be easy to understand.
This is why our own stock control solution features an intuitive interface and dashboard, providing all information in a digestible manner to best support workforces worldwide.
Why you need this: To empower your teams to use the system as intended, and feel its benefits to their day-to-day productivity.
4. Firm financial management
Of course, using a stock control system should carry its own financial benefits for your organisation, with research indicating that companies employing these solutions enjoy:
- 25% increase in productivity
- 20% gains in space usage
- 30% more efficient stock usage
But beyond this, a solid stock control solution will also have distinct financial management capabilities. We’ve already discussed the capacity to automatically trigger purchase orders when a particular asset or asset category falls below the acceptable threshold. This removes a burden on your financial team and makes sure any potential issue is dealt with instantaneously.
Furthermore, the system should allow you to make any changes to your pricing structures (both temporary and permanent) and stock costs when necessary. This enhances your ability to budget with confidence, and make immediate adjustments in relation to any trends or indicators your solution picks up on.
Why you need this: To increase overall operational efficiency and enhance the relationship between those responsible for inventory management and your financial team.
5. Integration with pre-existing software
When acquiring a stock control system, you don’t want this investment to be the catalyst for the cost of replacing your existing data assets and infrastructure. The solution should instead be able to seamlessly integrate itself with any current software or hardware you utilise, something that our own technology excels at.
Plus, to extend the functionality of your system even further, using it in tandem with dedicated Workforce Apps allows your workforce to capably monitor and control both your static and mobile stock from anywhere, at any time.
With this, you can reassure yourself that, regardless of time or location, your team has total insight into your stock levels, so you always stay well prepared and well supplied.
Why you need this: To guarantee that introducing stock control software doesn’t compromise your existing systems and technologies.
6. Remote management across multiple sites
If you are responsible for multiple sites, each with their own dedicated stock, the all-encompassing nature of a powerful stock control solution is even more valuable.
Bringing your distinct sites into one central platform not only allows you to more easily monitor stock levels across your entire organisation, but it also allows sites to help each other in times of difficulty. For instance, if one site has recently used their last of a certain asset, rather than immediately order a replacement, you can look across your sites to see if any have this asset spare.
Transferring assets between your sites might be a major cost-saver for your business in the long-term, saving you from unnecessarily splashing out on assets you already have to hand.
Why you need this: To manage stock across all locations without difficulty, and improve collaboration across your organisation.
7. Auditing and reporting capabilities
Finally, your stock control system should have the capacity to present custom-made reports, containing clear, valuable data to guide the present and future of your inventory management.
From compiling histories of your most and least frequently used items, to detailed snapshots of your present position, these reports should help you forward-plan your stock requirements well in advance, boosting your operational efficiency.
For retailers, the data in these reports may also inspire decisions on what assets might benefit from being discounted if their sales are lower than anticipated, as well as guide you on what popular items you should be investing in more heavily in future.
In addition, a stock control platform with built-in audit function will allow your team to examine any weaknesses to your existing approach to inventory management before they become critical issues, so you can invest your budget into the right areas.
Why you need this: To provide your team with the data they need to optimise your stock control as much as possible.
Find Success with the Right Stock Control Solution
As organisations take responsibility for more and more assets, each with different specifications and functions, the importance of an effective stock control system is more pronounced than ever.
Our Stock Control Module at MRI offers 360º visibility across your entire inventory, whether this is found in a single site or multiple locations. Providing accurate, up-to-the-minute stock information, our system ensures that costs are contained, actions are automated and your team is prepared for any eventuality.
Gain total visibility, tracking and management – talk to our team today.
Compass Group Case Study
Introduction Nicholas Ross, the CAFM and Hub Manager at PPP-IML, part of Compass Group UK& Ireland Ltd., shares his experiences transitioning from a legacy solution to MRI Evolution. His journey highlights the transformative impact of MRI Evoluti…
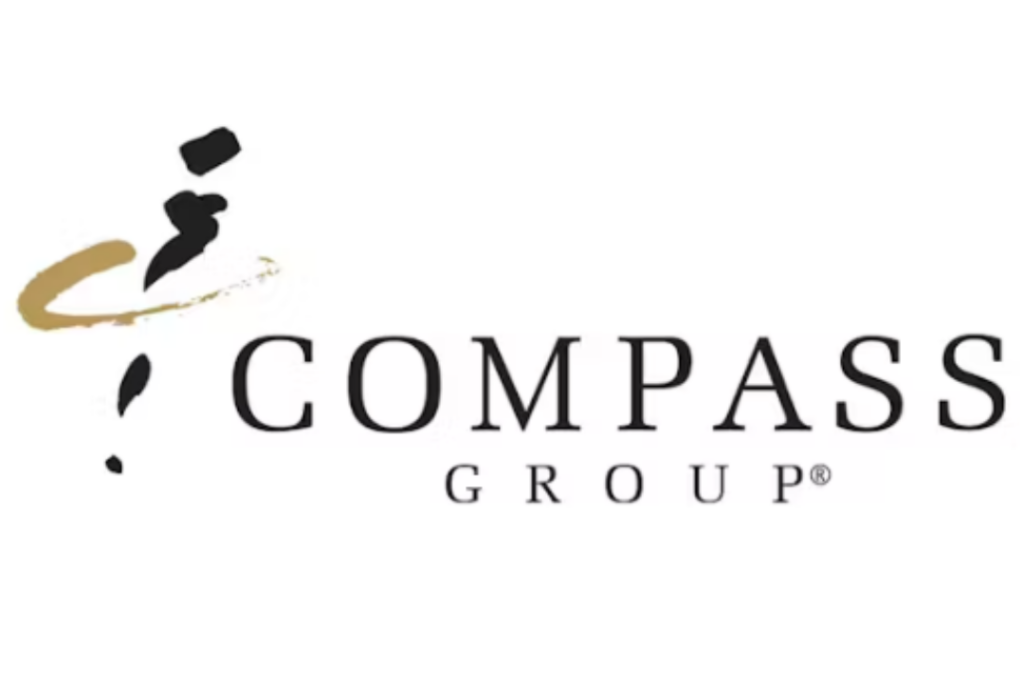